Build a Compact Uncoiler Feeder with Double Stage Leveler Machine for Car seat slides
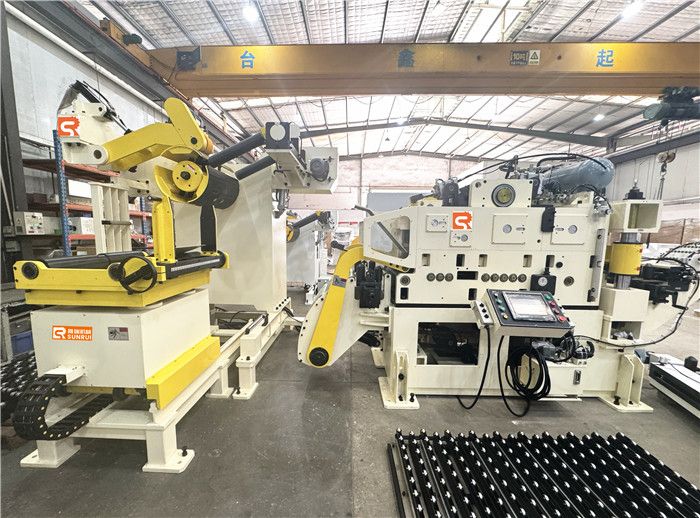
Compact coil feed line MFL4-600GF
Applicable Material: High tension steel
Yield Strength: ≤630 N/mm2
Coil Width: 100-600 mm
Coil Thickness: 0.6-6.0 mm
Straightener Rollers: 6pcs *(3 up/3 down) and 11 pcs*(6 up/5 down)
Leveling precision: 0.1 mm/m²
Max,. Loading weight: 5000kg
Working Speed: 0-22m/min
Customer Challenges---0.1 mm/m² leveling Precision
Our client, a manufacturer of guide rails for automotive applications, faced significant challenges to meet the stringent requirements set by international customers. The key difficulties included:
High Precision Requirement: The foreign client demanded that the stamped guide rail components achieve a flatness tolerance of 0.1 mm/m², which is a critical specification for their applications. Meeting this requirement was crucial for ensuring the functionality and reliability of the seat slides.
Material Variability: The varying thicknesses and materials used in producing seat slides added complexity to the leveling process, making it difficult to consistently achieve the desired flatness across different batches.
SUNRUI Solution---Compact Uncoiler Feeder with Double Stage Leveler Machine
To address these challenges, we devised a comprehensive solution centered around the implementation of a double-stage leveler machine, which included:
Coarse Leveling Rollers: The first set consists of 6 sets leveling rollers, which are designed to perform major flattening of the material. This stage handles the initial leveling process, allowing for the removal of significant warps and irregularities in the coil.
Precision Leveling Rollers: The second set includes 11 sets precision leveling rollers, which fine-tune the flatness of the material. This configuration allows for precise adjustments, ensuring that the final product meets the stringent 0.1 mm/m² flatness requirement.
Integration of Advanced Control Systems: We incorporated advanced sensors and feedback mechanisms that monitor the leveling process in real-time. The system automatically adjusts the roller pressure and alignment based on the material thickness and type, ensuring consistent quality throughout the production run.
Automated Workflow: The entire coil feed line is integrated with a PLC (Programmable Logic Controller) for automation, allowing for efficient operation and minimal human intervention. The HMI (Human-Machine Interface) provides operators with an intuitive interface to monitor and control the process easily.
Implementation Steps
Equipment Selection
Coil Feed Unit: A compact coil feeder with automatic threading capabilities to reduce setup time.
Double Stage Leveler: A machine featuring both coarse and precision rollers, designed to meet the required flatness specifications.
Hydraulic shear machine: It's used to cut the heads and tails of coils and ensure the flatness and quality of the finished products.
System Integration
The coil feed unit feeds the material into the double stage leveler.
The coarse leveling stage utilizes the six rollers to remove major warps, followed by the precision leveling stage with eleven rollers to achieve the desired flatness.
Testing and Calibration
Conduct a series of tests to calibrate the roller settings. This includes adjusting roller pressure and alignment based on material type and thickness.
Perform flatness testing on produced parts using laser measurement systems to ensure specifications are met.
Results
After implementing the compact coil feed line with the double-stage leveler, the following results were observed:
Improved Flatness: Achieved a flatness tolerance of 0.1 mm/m², surpassing the initial objective and meeting the stringent requirements of the client.
Space Utilization: The compact design saved approximately 20% of the original floor space required for the feed line.
Increased Throughput: Production rates increased by 30%, allowing for higher volume output without compromising quality.
Conclusion
The development of a compact coil feed line with a double-stage leveler machine has proven to be a successful endeavor in enhancing the precision of automotive parts manufacturing, particularly for guide rails. By focusing on efficient design, advanced technology integration, and rigorous testing, the project not only met but exceeded its objectives. This case study demonstrates the importance of innovation and precision engineering in maintaining high standards in manufacturing processes, ensuring that our client can meet their customers'stringent requirements effectively.