Coil feed line with double decoiler machine work with mechanical press machine for Automotive stamping parts
Coil Feed Line With Double Decoiler Machine For Automotive Stamping Parts
This is customized coil feed line which is required by our customer.Considering more efficient and safer work, we recommend the high Strength coil feed line with double decoiler machine to our customer and it's highly recognized by our customer. Sunrui machine always can provide the suitable and professional solutions for your sheet metal stamping application.
High Strength coil feed line with double decoiler machine with high automation that improves work efficiency, the double decoiler part can help change the coil more convenient and quickly.
Firstly, the coil car will load the coil and fixed the coil on the spindle of decoiler part, When it's in the automatic operation, supporting shaft of the inner diameter of decoiler through the loop control to make the main shaft intermittent rotation uncoiling .This machine is carrying with 2 sets of decoiler expansion mechanism, two sets of decoiler head can automatically rotate together with the frame by pressing the switch button, 2 sets of expansion mechanism used for automatic uncoiling and uncoiling preparation, when a coil on a decoiler head is uncoiling and refueling outage, another decoiler head which is standing by with a new coil can be used immediately after rack rotating movement, this structure can shorten the time of coil replacement cycle.
Basic Parameter For Coil Feed Line With Double Decoiler Machine
Coil Feed Line With Double Decoiler Machine MFL3-1000D | |||||||||||||||||||||||||||||||
Applicable material | S420MC, S315MC, HR4 | ||||||||||||||||||||||||||||||
Material strength | Yield strength≤681MPa | ||||||||||||||||||||||||||||||
Suitable Coil Width | 100-1300mm | ||||||||||||||||||||||||||||||
Applicable material thickness | 0.5-3.5mm | ||||||||||||||||||||||||||||||
Feeding length | 0-500mm | ||||||||||||||||||||||||||||||
Inside coil diameter | 470-520mm | ||||||||||||||||||||||||||||||
Max.coil outside diameter | Φ1200mm | ||||||||||||||||||||||||||||||
Max.coil weight | 7000kgs Per Side | ||||||||||||||||||||||||||||||
Speed | 30m/min | ||||||||||||||||||||||||||||||
Condition temperature | -10℃ - 45℃ | ||||||||||||||||||||||||||||||
RH | ≤95% | ||||||||||||||||||||||||||||||
Power | AC380V±10%,50HZ ±2% ,3PH ,5 Lines (can be changed according to your requirement) | ||||||||||||||||||||||||||||||
Pneumatic pressure | 0.5Mpa | ||||||||||||||||||||||||||||||
Running direction | From left to right |
Main part For Coil Feed Line With Double Decoiler Machine
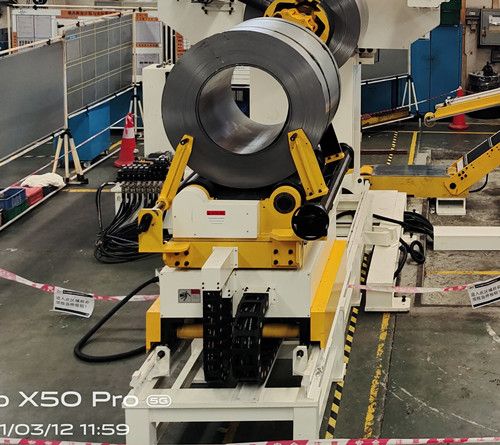
Coil Car
It is used to transfer the material coil to the main shaft of the decoiler rack.
Coil car with roll can help the coil strips enter the leveling machine smoothly when the material is involved.
The Coil car is provided with the material coil anti-tilt baffle, which can effectively prevent the material coil dumping when the coil is transferred to the smaller or narrow coils.
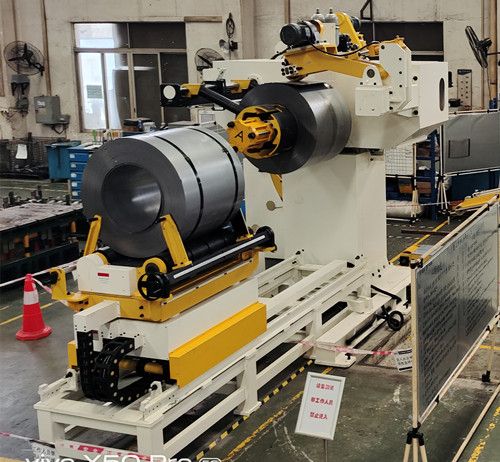
Dual Decoiler
With 2 sets of decoiler frame for a quick coil change
Hydraulic expansion for loading the coil
Varible Speed Control
Automatic rotota the decoiler head by pressing the button
Ultrasonic displacement sensor is used to detect the change of material diameter to adjust the pressure wheel and uncoiling speed synchronization.
Infrared photoelectric induction switch brings feedback signal through the induction material to control the start and stop of the main shaft of the uncoiler to ensure that there is enough reasonable buffer arc between the uncoiler and the leveling feeder
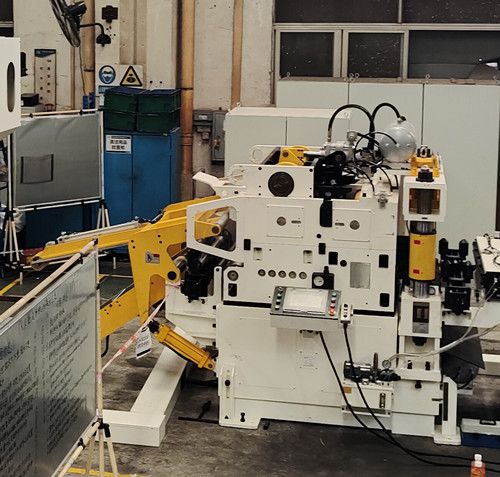
Straightener Feeder
The straightener-feeder part of coil feeding line leveling the coil set and feed it into stamping press in a fixed quantity. It has two inlet pinch rolls, both of them are motorized, which can clip the sheet strip and avoid material scratch.
11pcs (up6/down5) High quality straightener rollers which is carbon chroming bearing steel GCr15, with hardness HRC 60±2 for strength leveling and long-term service
Electric straightening setting adjusted by gear motor, setting accuracy 0.1mm, with touch screen control and automatic memory function.
Electronic servo control system with the pneumatic pilot release, it can ensure a high accuracy feeding.
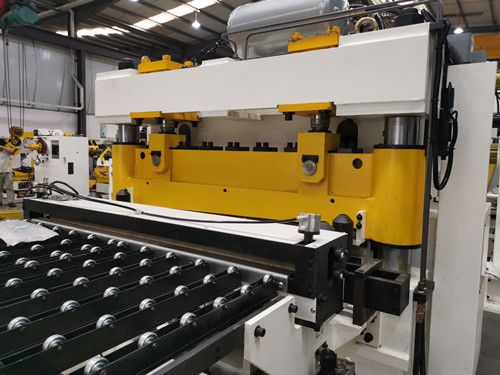
Hydraulic Shear
The hydraulic shear is mainly used for cutting the material head and tail of a certain length that do not meet the requirements of use, and the waste material after cutting is collected and transported away from the production line.
Hydraulic drive, touch screen button operation, go up and down with limit induction switch.
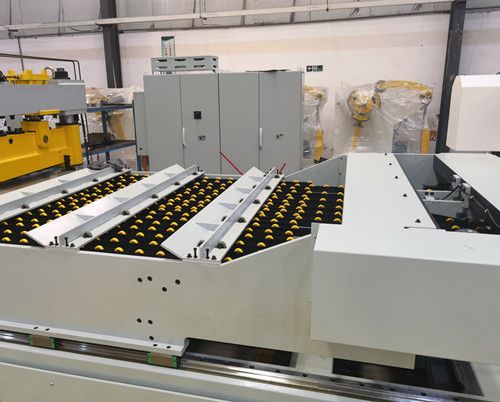
Tail Feeding device
There is a telescopic tail feeding device at the end of the feeder outlet. When the tail reaches the main servo feeding device, the control system controls the roller closure of the micro feeder, the front end of the feeder roller is opened, and the tail feeding roller is sent into the mold
production.
The tail feeding device has the electric telescopic function. When extended, it can be close to the edge of the die to maximize the utilization of the coil strips, and when retracted, it can reach the outer edge of the working table plate.
Wear-resistant Foley wheel is installed on the supporting frame to ensure the reliable transmission of the coil strips to the press mold after the sizing. The supporting frame of the micro feeder is arranged across to ensure the continuous support of the coil strips when it is telescopic.
Video