Enhancing Efficiency with NC Servo Feeder RNC-800 in Manufacturing
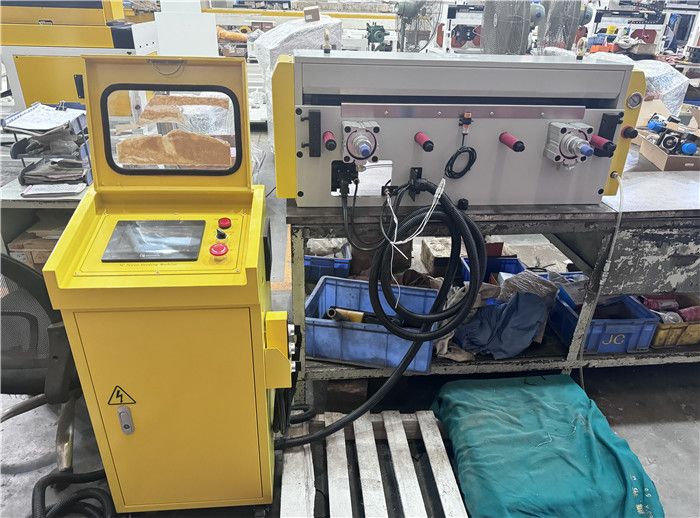
The Challenge
The primary challenge was to improve the efficiency and accuracy of the feeding process. The mechanical feeders often caused bottlenecks in the production line due to their inability to adapt to varying production demands. Additionally, the inconsistency in feeding speeds led to material wastage and increased production costs.
Solution
After a thorough evaluation of available options, the plant management decided to invest in servo feeders. Servo feeders are known for their precision, flexibility, and efficiency. Unlike mechanical feeders, servo feeders use advanced servo motor technology to control the feeding process with high accuracy.
Implementation
The implementation process involved several key steps:
Assessment and Planning: The first step was to assess the specific needs of the production line. This included determining the types of materials to be fed, the required feeding speeds, and the integration with existing machinery.
Selection of Servo Feeders: Based on the assessment, the plant selected servo feeders that offered the necessary features, including adjustable feeding speeds, easy integration, and robust construction.
Installation and Calibration: The servo feeders were installed and calibrated to ensure optimal performance. This involved setting up the control systems, programming the feeding parameters, and conducting initial test runs.
Training: Staff were trained on the operation and maintenance of the new servo feeders to ensure smooth adoption and minimize downtime.
Results
The implementation of servo feeders yielded significant improvements in the plant's operations:
Increased Efficiency: The servo feeders' ability to adjust feeding speeds in real-time allowed for a more consistent and efficient production process. This reduced bottlenecks and increased overall throughput.
Enhanced Precision: The high accuracy of the servo feeders minimized material wastage and improved the quality of the finished products.
Flexibility: The servo feeders' versatility in handling different materials and thicknesses provided the plant with greater flexibility in its production capabilities.
Reduced Maintenance: Compared to mechanical feeders, servo feeders required less frequent maintenance, leading to lower operational costs and reduced downtime.
Challenges and Solutions
Despite the numerous benefits, the implementation was not without challenges. One of the main issues was the initial cost of the servo feeders, which was higher than that of traditional mechanical feeders. However, the long-term savings in terms of reduced material wastage and maintenance costs justified the investment.
Another challenge was the initial learning curve for the staff. The advanced technology of the servo feeders required a period of adjustment. Comprehensive training and ongoing support helped mitigate this issue, ensuring a smooth transition.
Conclusion
The case of this automotive parts manufacturing plant demonstrates the transformative impact of servo feeders on production efficiency and precision. By investing in advanced feeding technology, the plant was able to overcome the limitations of traditional mechanical feeders, resulting in significant operational improvements. While the initial costs and learning curve posed challenges, the long-term benefits far outweighed these hurdles. This case study serves as a testament to the value of embracing modern technology in the pursuit of manufacturing excellence.
Servo Feeder RNC-800 is working in customer's factory