High-Precision Leveling Coil Feed Line for Automotive Brake Pad Production
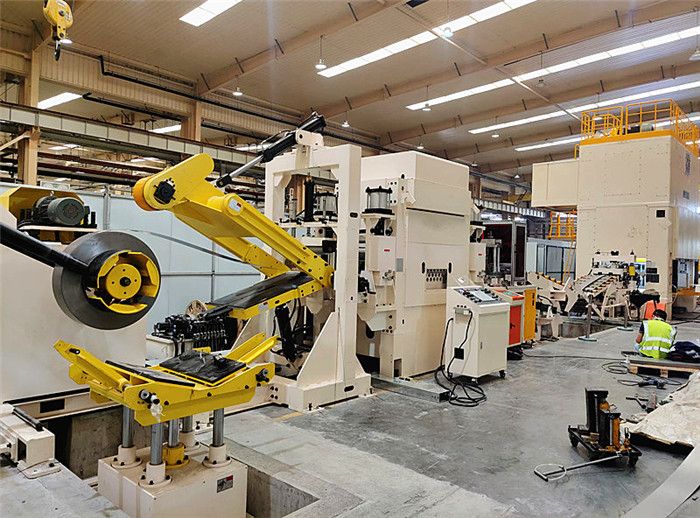
A leading first-tier automotive supplier specializing in high-performance brake pads required a coil feeding line with exceptional leveling precision to ensure consistent material flatness and dimensional accuracy. The brake pads, made from cold-rolled steel (2.5–8.0mm thickness), demanded tight tolerances (±0.15mm) to meet stringent safety and performance standards.
SUNRUI Solution---High-Precision Leveling Coil Feed Line
1. Complete System Integration
The system includes a Decoiler, a 6 HI Straightener Machine, a Loop Device, an NC Servo Feeder, a Hydraulic Shear, and an Automatic Oil Machine, creating a fully automated coil feeding line that ensures high precision and efficiency for the production of brake pads.
2. High-Precision Leveling
6 Layer Strcuture with 11-Level Precision Leveling Rollers and universal jonit drive: The system features 5 upper and 6 lower hardened chrome-plated rollers (HRC60±2) that effectively eliminate material warping, achieving flatness of ≤1.5mm/m².
The straightener features a 6-high configuration, which enhances the flattening process by providing multiple points of contact with the material. This structure allows for greater control and precision in leveling, resulting in superior flatness and reduced defects.
Universal Joint Drive: The straightener is equipped with a universal joint drive system, which offers several advantages:
Improved Flexibility: The universal joint allows the straightening rollers to adapt to various angles and positions, ensuring consistent pressure is applied across the material, regardless of its thickness or shape.
Enhanced Torque Transmission: This design efficiently transmits torque from the motor to the rollers, reducing energy loss and increasing the overall efficiency of the straightening process.
Reduced Wear and Tear: The flexibility of the universal joint minimizes strain on the components, leading to longer service life and reduced maintenance costs.
Electric Adjustment: The leveling system allows for fine adjustments with an accuracy of 0.1mm, displayed via a dial gauge, ensuring repeatable results for varying material thicknesses (2.5–8.0mm).
Hydraulic Shear:The hydraulic shear is integrated into the line for precise cutting of materials to required lengths. Its advantages include:
High Cutting Precision: The hydraulic system provides consistent and accurate cuts, essential for maintaining tight tolerances in brake pad production.
Increased Speed: The shear operates quickly, allowing for efficient workflow and reduced cycle times.
Minimized Burr Formation: The design reduces burrs and ensures clean edges, which is vital for quality control.
Automatic Oil Machine:The automatic oil machine ensures that all moving parts of the system are adequately lubricated, enhancing operational efficiency and extending machinery life. Key benefits include:
Consistent Lubrication: Automated lubrication minimizes downtime for maintenance and ensures that all components operate smoothly.
Reduced Wear and Tear: Proper lubrication reduces friction, thereby extending the lifespan of mechanical components.
Enhanced Safety: By reducing the need for manual lubrication, the automatic oil machine decreases the risk of accidents in the workplace.
Servo-Driven Feed System:
AC Servo Motor: A 5.5KW AC servo motor provides ±0.15mm feed accuracy over 500mm lengths at a speed of 16m/min, synchronized with press cycles to enhance operational efficiency.
Overbridge Device: This mechanism maintains tension control, preventing material deformation during intermittent feeding, thus safeguarding the integrity of the material.
3. Automated Material Handling:
Decoiler: The decoiler automatically unwinds coils, allowing for smooth and efficient feeding into the leveling and straightening process.
Loop Device: Given the significant thickness and yield strength of the materials, the integration of a loop device is crucial. It enables automatic material threading, eliminating the need for manual intervention. The loop device also allows for a pit installation, accommodating the inertia of high-strength materials and ensuring seamless operation.
NC Servo Feeder: The NC servo feeder precisely delivers the material to the next stage of production, enhancing overall throughput and accuracy.
Results
Quality: The system achieved a consistent flatness of ±0.1mm, which is critical for producing high-quality brake pad laminates.
Efficiency: The fully integrated line operates at 80 strokes per minute, reducing cycle time by 30% compared to manual feeding processes.
Cost Savings: The automation allowed for the reduction of personnel from 3 operators to just 1 per line, alongside a 15% decrease in material waste.
Enhancing SUNRUI's Competitive Advantage:
SUNRUI Machinery Co., Ltd. stands out in the industry not only for its precision engineering but also for its commitment to innovation and customer satisfaction. The integration of advanced technologies enhances the overall performance and reliability of their machinery. Key advantages include:
SUNRUI's systems are built with high-quality materials and components, ensuring long-term reliability and reduced maintenance costs.
User-Friendly Interface: SUNRUI offers tailored solutions to meet specific customer requirements, further enhancing operational efficiency and production quality.
Advanced 6 HI Straightener Machine Benefits:
Superior Flattening Capability: The 6 HI straightener provides exceptional flattening capabilities, crucial for demanding applications such as brake pad production.
Flexibility for Various Thicknesses: Capable of handling a wide range of material thicknesses, it is ideal for diverse production runs and can adapt to changing manufacturing needs.
Consistent Performance: The design ensures uniform pressure distribution across the material, resulting in consistent flatness and reduced defects, thereby improving the quality of the final product.
Conclusion:
SUNRUI's innovative leveling feed line solution exemplifies how precision engineering can elevate automotive brake pad manufacturing. By combining accuracy, automation, and reliability with the benefits of advanced technology and machinery—including the decoiler, 6 HI straightener, loop device, NC servo feeder, hydraulic shear, and automatic oil machine—SUNRUI positions itself as a leader in the automotive parts manufacturing sector. This case study not only showcases the effective application of SUNRUI's technology but also emphasizes the importance of precision and efficiency in meeting the stringent demands of the automotive industry, particularly for first-tier suppliers who prioritize quality and safety in their production processes.