Implementing a Coil Feed Line with Decoiler Straightener and NC Servo Feeder for Stamping Small Metal Parts
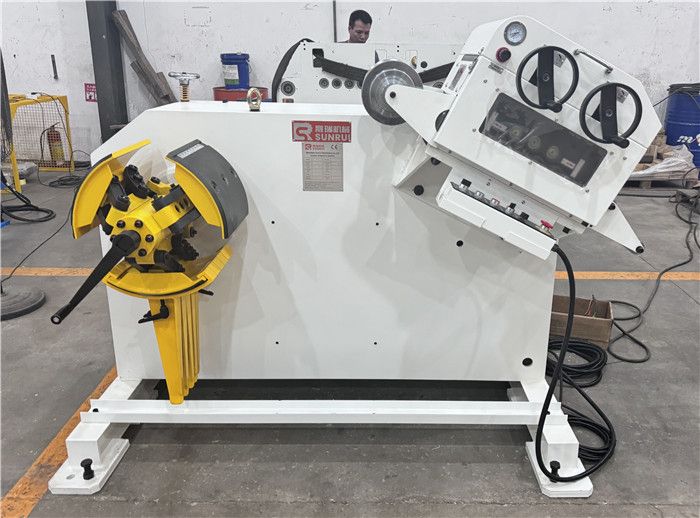
Background
The manufacturing facility produces small metal components for the automotive and electronics industries. Prior to the upgrade, the facility relied on manual feeding systems and semi-automated equipment, which resulted in inconsistent material feeding, frequent downtime, and high material wastage. The increasing demand for precision parts necessitated a more advanced and automated solution.
Furthermore, the existing punch press machine is an outdated model. Based on the appearance of the customer's punch press, we customized an NC servo feeder suitable for installation on the punch press.
The Challenge
The primary challenges faced by the facility included:
Inconsistent Material Feeding: Manual feeding led to variations in material positioning, causing defects in stamped parts.
Material Wastage: Improper handling of coils and misalignment during feeding resulted in significant material loss.
Downtime: Frequent adjustments and maintenance of the old system disrupted production schedules.
Lack of Flexibility: The existing system could not easily adapt to different material thicknesses or coil widths.
To address these issues, the facility decided to invest in a fully automated coil feed line with decoiler straightener and NC servo feeder.
The Solution: Coil Feed Line with Decoiler, Straightener, and NC Servo Feeder
The new system was designed to automate the entire material feeding process, from coil loading to precise feeding into the stamping press. Key components of the system included:
Decoiler: Automatically unwinds the metal coil and feeds it into the straightener.
Straightener: Ensures the metal strip is perfectly flat and free of curls or bends before feeding.
NC Servo Feeder: Provides precise, programmable control over the feeding process, ensuring accurate material positioning for stamping.
Implementation
The implementation process involved the following steps:
System Design and Customization: The coil feed line was customized to handle the specific material types (e.g., steel, aluminum) and thicknesses used in the facility. The NC servo feeder was programmed to accommodate various part designs and production requirements.
The stamping press machine in custo,er's factory which is an older model featuring triangular support brackets on both sides and a glass protective cover. Given the limitations of the machine, we understand that installing a feeder directly onto the press machine is not feasible. To address this, we have designed a floor-standing servo feeder that integrates seamlessly with the existing setup. This customized servo feeder includes an extended discharge frame to facilitate the smooth introduction of coil strips into the punch press machine and molds. We believe this solution will enhance the efficiency of operations while ensuring safety and ease of use.
Installation and Integration: The system was installed and integrated with the existing stamping press. Special attention was given to aligning the decoiler, straightener, and servo feeder to ensure smooth material flow.
Testing and Calibration: The system was tested with different coil sizes and materials to ensure optimal performance. The NC servo feeder was calibrated to achieve precise feeding lengths and speeds.
Training: Operators and maintenance staff were trained on the new system to ensure efficient operation and troubleshooting.
Results
The implementation of the coil feed line delivered significant improvements in production efficiency and product quality:
Improved Precision: The NC servo feeder ensured accurate material positioning, reducing defects in stamped parts by 30%.
Reduced Material Wastage: The straightener eliminated material curls and bends, reducing material wastage by 20%.
Increased Productivity: The automated system reduced downtime and increased production speed by 25%.
Enhanced Flexibility: The programmable NC servo feeder allowed for quick adjustments to accommodate different part designs and material specifications.
Lower Labor Costs: Automation reduced the need for manual intervention, lowering labor costs and minimizing human error.
Challenges and Solutions
While the new system delivered impressive results, the implementation process was not without challenges:
Initial Investment: The cost of the coil feed line was significant. However, the long-term savings in material, labor, and increased productivity justified the investment.
Learning Curve: Operators required time to adapt to the new system. Comprehensive training and ongoing support helped overcome this challenge.
Maintenance Requirements: The advanced system required regular maintenance to ensure optimal performance. A preventive maintenance schedule was established to address this issue.
The implementation of a coil feed line with a decoiler, straightener, and NC servo feeder transformed the facility's metal stamping process. By automating material feeding and ensuring precision, the system significantly improved efficiency, reduced costs, and enhanced product quality. This case study highlights the importance of investing in advanced automation technologies to stay competitive in the manufacturing industry.For manufacturers facing similar challenges, adopting a coil feed line with an NC servo feeder can be a game-changer, enabling them to meet the growing demands for precision and efficiency in metal stamping.