Compact Coil Feed line MFL4 (0.6-6.0mm)
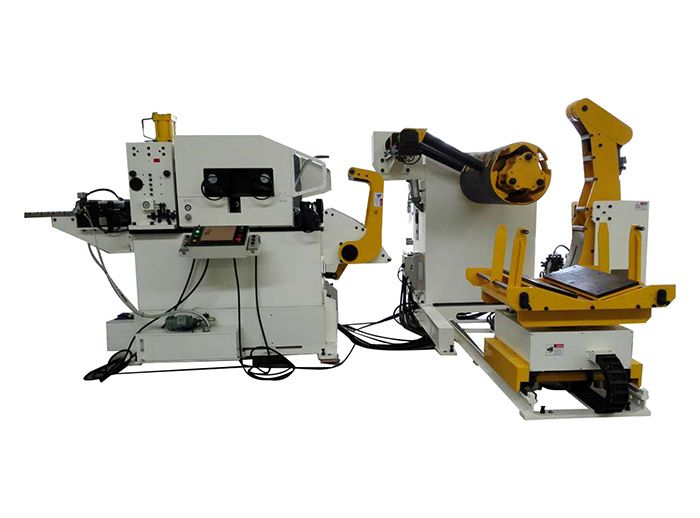
Applicable Material
Raw Material Type: Hot-Rolled Metal steel, Cold-Rolled Metal steel, Galvanized Metal steel, Stainless Steel etc.
Coil Width: 100-1600 mm
Material Thickness: 0.6-6.0 mm
Yield Strength: ≤245 N/mm2
Tensile Strength: ≤392 N/mm2
Working Speed: 0-22m/min
Brief Profile of Compact Coil Feed line
The Compact Coil Feeding Line is a highly efficient machine that combines the functions of a decoiler, a straightener, and a feeder into one compact unit. The machine is positioned directly at the press, which saves space typically required by a material loop of straightened material.
The feeding line is supplied with material from a small loop of not straightened material located below the decoiler. The decoiler is equipped with a variable speed drive and a highly sensitive loop control to ensure there is always enough material available for supply to the straightener-feeder.
If feeding lengths and stroke rates require a larger material stock within the material loop, the Compact Coil Feeding Line can be completed with a loop pit. Our Coil Processing Systems can handle coil material widths ranging from 400mm to 1600mm, coil thickness from 0.6mm-6.0mm, and coil weights of up to 20,000kg.
The Compact Coil Feeding Line is designed for the production of thick auto parts, such as brake pads, front pillars, seat slide rails, center pillars, flip wheels, and more. Its compact design helps minimize floor space requirements while maintaining high levels of efficiency, precision, and capability in the production process.
Application of Compact Coil Feed line
● AUTOMOTIVE
Manufacture of equipment for metal stamping of automotive parts. Structural car body parts and other parts like front brackets, brake pads, wipers, seat supports, electrical windows, exhaust pipes, catalytic converters, radiators, levers, pedals, gear box parts, wheels, damping supports, etc ...
● BUILDING & HOUSEHOLD
Feeding lines to produce a variety of metal components for the building and household sector and derivatives. Parts like braces, clamps, straps, locks and hinges for doors,furniture hardware, knifes, cooking ware carpentry parts, metal supports, perforated plates, etc ..
● HOME APPLIANCE & ElECTRONICS
Installations for the manufacture of parts for household appliances sector or white goods. Metal pieces like motor housings, doors,electric cabinet, shells and covers, trays, guides, caps, supports, brackets, handles, etc ...
● ILLUMINATION
Many solutions for the blanking of metal parts for lighting sector. Several parts such as housings, panels, brackets, feet, arms, buttons, diffusers, etc ...
Features of Compact Coil Feed line
● Space-saving, easy installation and low maintenance
Compact design is ideal for limited space metalworking stamping process.
The compact coil feeding line is very easy to install, which can enter into mass production in a short time. Without a long material loop, the coil feeding line length is usually no more than 5m, some models such as MFL2 is only 3m length, which will save workplaces of stamping room. Thanks to the international brand core components, automatic lubrication system and self-inspection procedures, the compact coil feeding line have a very low failure rate and easy to maintenance.
What’s more, until now the machine which we sold has few after-sales problems.
● Modular control, simple and smart operation
Compact coil feeding machine is not only a simple combination of decoiler, straightener, and feeder machine into one unit, but also highly integrated control in operations. Easy to operate and maintain. Our machine adopts PLC control, all process parameters of products to be stamping can be set up and saved in program means that there is no need to repeat input, also with the characteristic of high degree of automation, high operation safety, low maintenance. Reducing labor input and improve the production efficiency. Moreover, movable regulating handle is very convenient operation for installing and debugging when the machine is testing.
● Advance Techniques
With the world’s leading automatic metal forming stamping techniques ,advanced and humanized management system, we unite thousands of elites dedicated to the development of automatic press,including top engineers in this field,experienced technicians, production workers with fine craftsmanship to ensure every equipment produced durable, high-efficiency and stable.
● Reliable Structure Design
Super large scale and plenty of advanced quality control measures including CNC machining, grinding machine, boring machine and Lathe machine equipment and various precision testing instruments from Germany, Japan and Taiwan. It can ensure the high precision and quality of all parts of machine.
What's more, all of main body makes surface treatment with our shot blasting machine before they are painted. With our shot blasting machine treatment, the machine surface is excellent for painting.they blast onto the surface of work piece with shots to clean and beautify the surface. The shot blasting also enhances the pressure stress of work piece surface and extends the lifespan.We also use high-end vehicle oil paint for our machine to have high level of painting quality and you don’t need to worry about broken painting problem under extremely nasty working environment.
● High precision straightening and feeding performance
With the coil inlet supporting arm assisting, the strip head will be inserting into the straightener part automatically and smoothly, and driven by gear transmission, the strips will be straightening and feeding forward.
The straightener roller and feeder roller mechanism are placed on the same precise platform to ensure the uniformity of parallel precision and to limit the error of leveling and feeding operation to the maximum extent.
● Wide range of metal coil stamping application
Compact coil feeding line is design to make thick plate of auto parts stamping, such as brake pads, front pillar, Seat slide rail, center pillar, flip wheel and so on.
Also for hardware stamping parts, furniture and home appliances and so on.
Specification of Compact Coil Feed line
Model | MFL4-400 | MFL4-500 | MFL4-600 | MFL4-800 | MFL4-1000 | MFL4-1300 | MFL4-1600 |
Stock Width(mm) | 70~400 | 70~500 | 70~600 | 70~800 | 70~1000 | 70~1300 | 70~1600 |
Stock Thickness(mm) | 0.6~6.0 | ||||||
Max.Coil Weight(kg) | 5000 | 5000 | 5000 | 7000 | 7000 | 10000 | 15000 |
Max.Coil O.D.(mm) | 1400 | ||||||
Coil I.D.(mm) | φ470-520 | ||||||
Feed Length(mm) | ~500* | ||||||
Max.Line Speed(m/min) | 16~24 | ||||||
Straightener Rolls(piece) | φ68mm*7(upper4/ lower 3) | ||||||
Feed Rolls (piece) | φ88mm*2 (upper 1/ lower 1) | ||||||
Back-up Rolls (piece) | φ68mm*220mm*3 Groups | ||||||
Servo Motor | AC5.5 | AC5.5 | AC7.5 | AC7.5 | AC11 | AC11 | AC15 |
Mandrel Expansion | Hydrauilc | ||||||
Reel Motor(kw) | 2.2 | 2.2 | 2.2 | 5.5 | 5.5 | 7.5 | 11 |
Power(v) | 3 Phase 220V/380V/440V/50HZ | ||||||
Operating Air(Mpa) | 0.49 |
Straightener Capacity( Yield strength σs≤245N/mm² ,Tensile strength σb≤392 N/mm²) | |||||||||||||
Model | Thickness(mm) | ||||||||||||
0.6 | 1 | 1.3 | 1.6 | 2 | 2.3 | 2.8 | 3.2 | 4 | 4.5 | 5 | 6 | ||
Width(mm) | MFL4-400 | 400 | 293 | 203 | |||||||||
MFL4-500 | 500 | 361 | 293 | 203 | |||||||||
MFL4-600 | 600 | 457 | 361 | 293 | 203 | ||||||||
MFL4-800 | 800 | 457 | 361 | 293 | 203 | ||||||||
MFL4-1000 | 1000 | 714 | 457 | 361 | 293 | 203 | |||||||
MFL4-1300 | 1300 | 933 | 714 | 457 | 361 | 293 | 203 | ||||||
MFL4-1600 | 1600 | 1170 | 933 | 714 | 457 | 361 | 293 | 203 |
Main Parts of Compact Coil Feed line
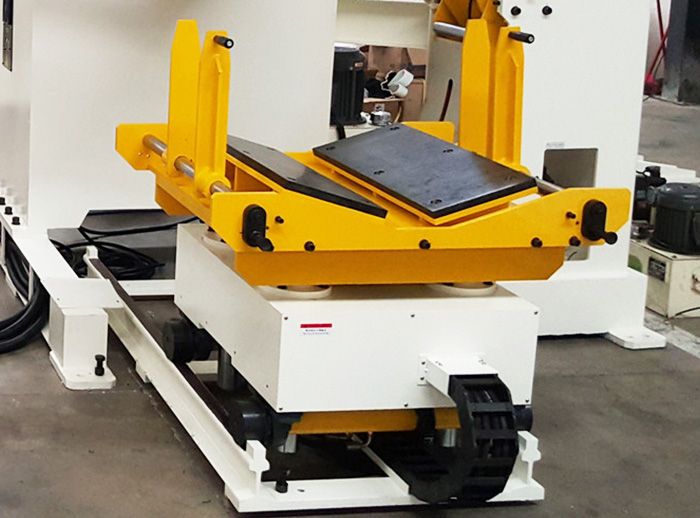
Coil Car
● The surface of Coil car is V type with sandblasting surface treatment process, it can protect the material surface from scratching and the main function is assisting loading the coils on the spindle rack of decoiler parts.
● Adjustable coil guide baffles prevent narrow coils from dumping
● Coil car move forward and backward by Hydraulic motor
● Coil car lifting up and down smoothly by hydraulic cylinder
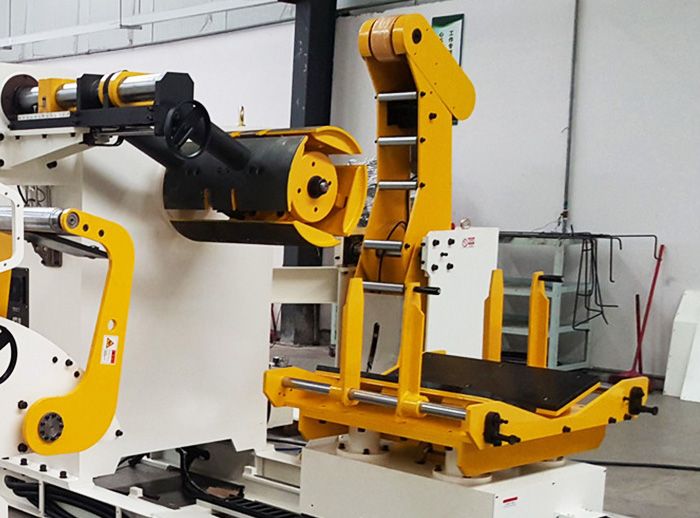
Decoiler Machine
● After the coils holds on the spindle of decoiler machine, be sure to press the press arm and hold on the coil strips, it is driven from its outside diameter via spindle.
● Hydraulic threading mechanisms and a hydraulically opening and closing straightening head, allow for safe and easy threading of even narrowest, thickest strip.
● Decoiler with support cantilever structure can loading up to 15ton. And there’re f hydraulic structure for uncoiler spindle expansion.
● Moreover, material auto-alignment function as an optional meet your requirements.
● Spindle expansion range: Φ470-Φ520mm.
● Decoiler is Driven is by AC motor with an inverter
● Press arm pressure is driven by AC motor
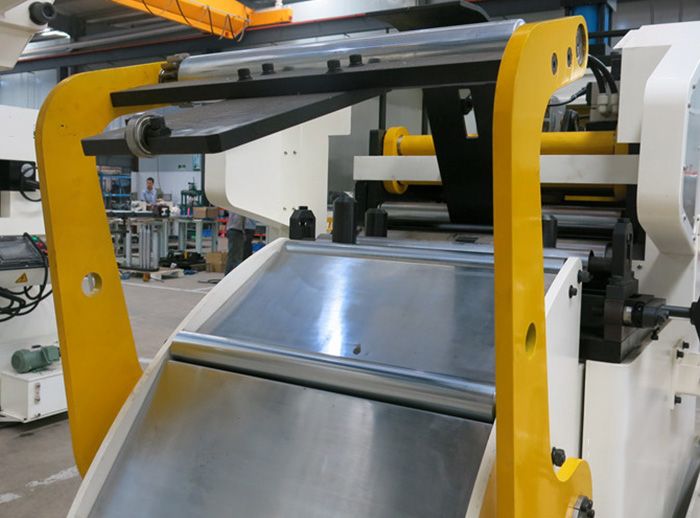
Coil Inlet Support Arm
● After uncoiling process, the support arm of decoiler machine will rise up and lead the material strips into coil inlet support arm which is driven by a hydraulic cylinder will close automatically to hold-down material strip when strip head touch the straightener part.
● The bottom inlet roller is geared transmission, sharing drive power with straightener rollers.
● When upper inlet roller goes down, the two rollers clamp the metal strip and lead it to the straightening part. These two rollers are made by high quality bearing steel, with sandblasting treatment, hardness reaches HRC60±2.
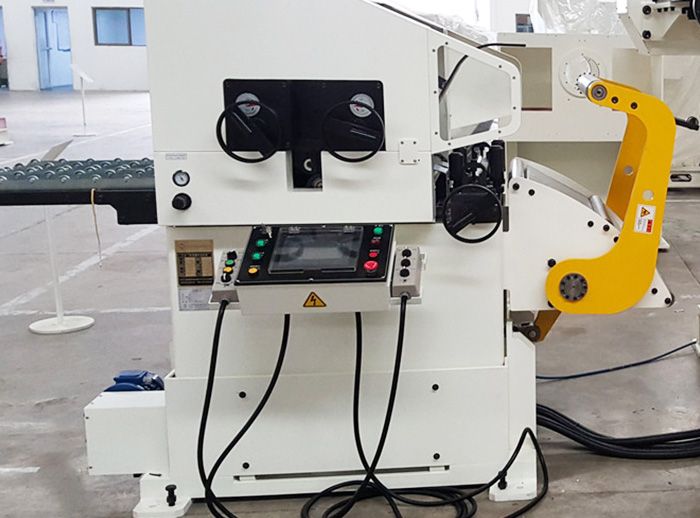
High Precision Straightening and Feeding Machine
● The straightener feeder parts is straightening the coil strips and feeding it into the stamping press and dies according to the fixed length controlled by PLC.
● Given the difference in coil at the beginning of rollers and the end of roller, it is usually necessary for an operator to always be monitoring straightening operations, and to manually carry out corrections to ensure a high degree of precision in straightening.
● With the unique electrically adjustment fitted on the MFL4 Series coil straightener-feeder, changes in the coil strips thickness are detected during production. Straightening correction is performed continuously and automatically. it making a significant contribution to operational efficiency.
● Moreover, additional backup roller can achieves a high precision straightening performance.
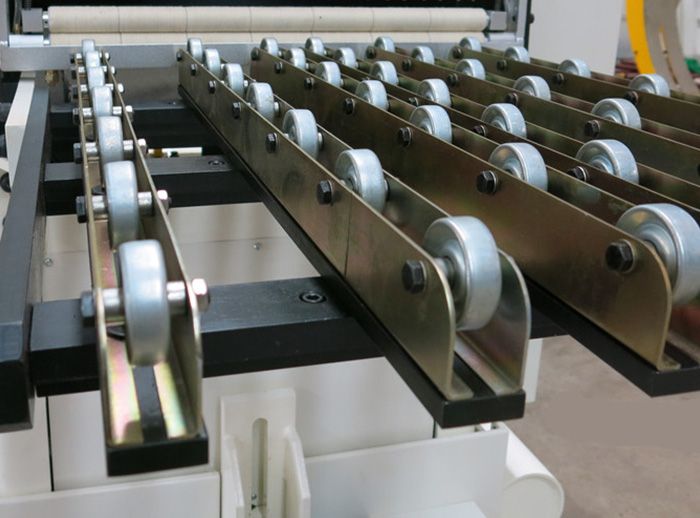
Discharging Support Bracket
● The outlet support bracket is used to deliver the straightening strips to press die smoothly.
● When the coil material is thin thickness or soft material , or the distance between straightener-feeder and stamping dies is long, the strip can not be delivered the strip head into the die successfully, the support bracket will help to reach it.
● The length of the support bracket is adjustable to meet different dimensions of stamping press machine and dies.
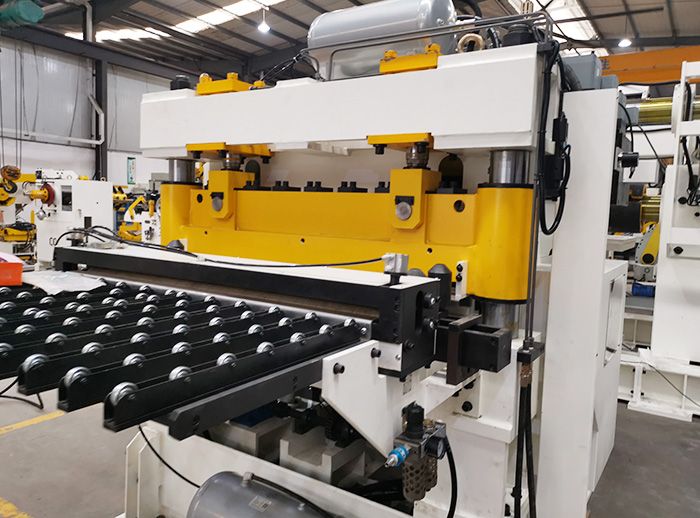
Hydraulic Shear Machine (Option)
● A hydraulic shearing unit is used to cut the material heads and tails for productivity improvement and better stamping product quality.
● The hydraulic cutting unit has four sides scissors to achieve smooth cutting.It's operated by touch screen control and with manual scissors adjustment.
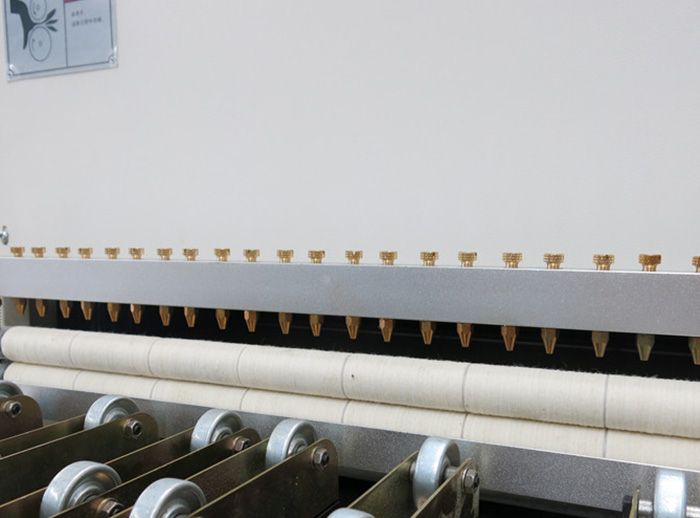
Automatic Lubrication Unit (Option)
● Lubrication of steel strip before stamping will protect the stamping dies from damaging and prolonging the uselife.
● The automatic lubrication system is automatically controlled, with an oil loop recycling system, which will save oiling cost and prevent leakage.
Video of Compact Coil Feed line