How to Adjust the Multi-Stage Mode of NC Servo Feeders
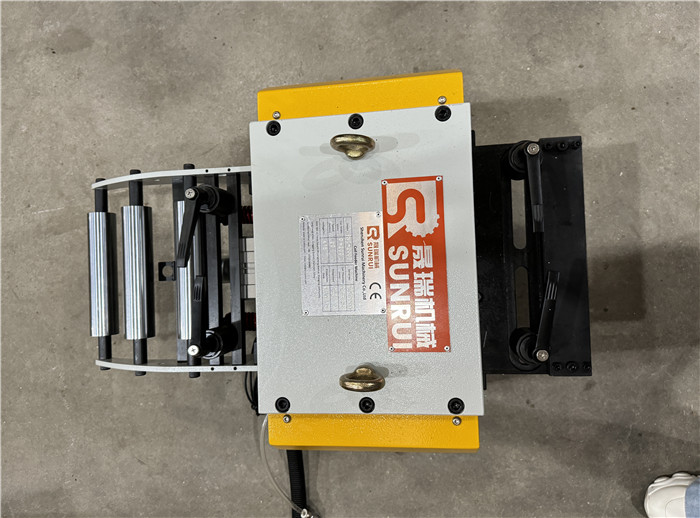
The NC servo feeder, as an automation device around stamping machines, has gained widespread application in recent years due to the rapid development of the new energy industry. To ensure that the equipment can effectively adjust according to different stamping materials (including width and thickness) and mold requirements, users need to fine-tune parameters such as feed height, material width, pressure springs, feeding angles, release angles, feeding length, and the number of feeds. Below are the specific steps for adjusting the multi-stage mode of an NC servo feeder.
The specific steps for adjusting the multi-stage mode of an NC servo feeder
1. Preparation Before Startup
Before starting the automated stamping production line, first, activate the decoiler and levelling machine. Slowly unwind the decoiler machine using the jog function, then manually pull the material head through the leveling machine. Meanwhile, the operator should input the feeding step length on the touch screen of the NC servo feeder and click on manual release, allowing the upper roller to rise and disengage from the lower roller, reaching a fully relaxed state. Finally, pass the straightened material head through the feeding roller of the feeder.
2. Adjusting the Material Guide Wheel
During the feeding process, ensure that the material head smoothly passes through the feeder and enters the stamping mold. Adjust the position of the material guide wheel on the loading rack according to the actual width of the material. The position of the guide wheel must match the actual width of the material. After securing the guide wheel, manually pull the material to ensure it moves smoothly without obstruction. If any blockage is detected, adjust the guide wheel position accordingly and check for any misalignment as the material enters the feeder, mold, and stamping machine.
3. Single Feed Testing
When performing single feed testing, the approach varies based on the width of the mold and material:
Situation 1: Small Mold and Material - When both the mold and the material are small and narrow, the NC servo feeder can skip the clamping action. Instead, manually pull the material completely into the stamping mold until it reaches the discharge opening, then allow the NC servo feeder to execute the clamping action. Finally, use the handle of the NC feeder to perform a single feed in conjunction with the incremental movement of the stamping machine.
Situation 2: Large Mold and Material - When the mold and material are wider, the manual pulling process can be cumbersome and labor-intensive. In this case, first, allow the NC servo feeder to execute the clamping action to securely hold the material, then use the jog handle on the NC servo feeder to feed the material slowly, followed by a single feed test.
Important Considerations
Adjusting the NC servo feeder is a meticulous and professional task. Operators must carefully adjust parameters based on actual stamping materials, mold requirements, and process characteristics. Additionally, if the NC servo feeder encounters sudden power outages or electrical circuit failures during operation, the machine will automatically halt, ensuring safety. The servo feeder is equipped with electrical and mechanical safety devices; in the event of a power failure, the brake will engage automatically to prevent accidental operation, allowing users to operate the machine with confidence.
Additional Insights
To enhance the efficiency and reliability of the NC servo feeder, regular maintenance and inspection are crucial. Operators should:
Conduct Regular Maintenance: Schedule periodic checks on the mechanical components, such as rollers and guide wheels, to prevent wear and tear that may affect feeding accuracy.
Monitor Electrical Systems: Ensure that all electrical connections are secure and that there are no signs of wear in the wiring, which could lead to operational disruptions.
Train Personnel: Provide adequate training for all operators to understand the machine's functions and safety protocols, minimizing the risk of operational errors.
Keep Records: Maintain logs of adjustments and maintenance activities to track performance over time and identify patterns that may indicate the need for further adjustments or upgrades.
By following these steps and considerations, operators can optimize the performance of the NC servo feeder, contributing to increased productivity and improved product quality in the stamping process.