The Ultimate Guide to Decoiler Machines
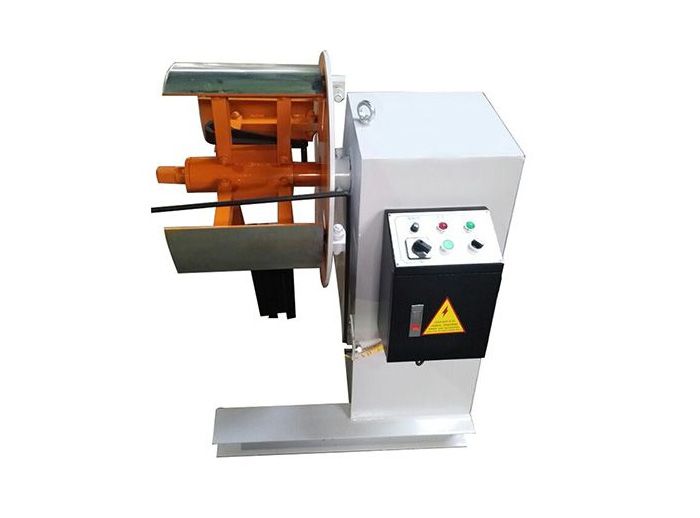
Decoiler machines are essential equipment used in the metalworking industry to uncoil large coils of metal material, such as steel or aluminum, into flat sheets or strips.
Decoiler machines are essential equipment used in the metalworking industry to uncoil large coils of metal material, such as steel or aluminum, into flat sheets or strips. Decoiling is the process of unwinding a coil of metal material to create a flat sheet or strip that can be further processed or fabricated into different shapes and sizes. In this guide, we will provide you with an overview of decoiler machines, their types, components, working principle, maintenance, and safety considerations.
Types of Decoiler Machines:
Decoiler machines are available in different types, depending on the size and weight of the coil to be uncoiled. Some common types of decoiler machines are:
Manual Decoiler Machines:
Manual decoiler machines are the simplest type of decoiler machines, and they rely on manual labor to uncoil the metal coil. They are suitable for small to medium-sized coils and are generally used in low-volume production environments.
Motorized Decoiler Machines:
Motorized decoiler machines use an electric motor to unwind the metal coil. They are faster and more efficient than manual decoiler machines and are suitable for medium to large-sized coils. Motorized decoiler machines can be further classified into two categories based on their operation:
a) Single-motor Decoiler Machines:
Single-motor decoiler machines have only one motor that drives the uncoiling process. They are suitable for lightweight coils and low-volume production environments.
b) Dual-motor Decoiler Machines:
Dual-motor decoiler machines have two motors, one to drive the decoiling process and the other to control the tension of the material being uncoiled. They are suitable for heavier coils and high-volume production environments.
Components of Decoiler Machines:
Decoiler machines are composed of several components that work together to uncoil the metal coil. Some essential components of decoiler machines are:
Mandrel:
The mandrel is a cylindrical shaft that supports the coil of metal material during the uncoiling process. The mandrel is usually mounted on bearings to reduce friction during rotation.
Brake:
The brake is used to control the tension of the material being uncoiled. It applies pressure on the mandrel to prevent the coil from unwinding too quickly.
Coil Holding Arms:
Coil holding arms are used to support the coil of metal material during the uncoiling process. They can be adjusted to fit the size of the coil and prevent it from slipping or tilting.
Decoiling Head:
The decoiling head is the part of the machine that contacts the metal coil and pulls it off the mandrel. The decoiling head can be customized to suit different types of material and shapes.
Working Principle of Decoiler Machines:
The working principle of decoiler machines is straightforward. The metal coil is placed on the mandrel and secured with coil holding arms. The brake is applied to control the tension of the material being uncoiled. The motor rotates the mandrel, and the decoiling head pulls the metal coil off the mandrel and uncoils it into a flat sheet or strip.
Maintenance of Decoiler Machines:
Proper maintenance of decoiler machines is essential to ensure their longevity and efficiency. Some tips for maintaining decoiler machines are:
Regular Lubrication:
The bearings, mandrel, and other moving parts of the machine should be lubricated regularly to reduce friction and prevent wear and tear.
Cleaning:
The machine should be cleaned regularly to remove dirt, dust, and other debris that can affect its performance.
Inspection:
The machine should be inspected regularly to identify any worn or damaged parts that need to be replaced.
Calibration:
The tension and speed settings of the machine should be calibrated regularly to ensure accuracy.
Click here for all our contact info.