The Ultimate Guide To Servo Feeder
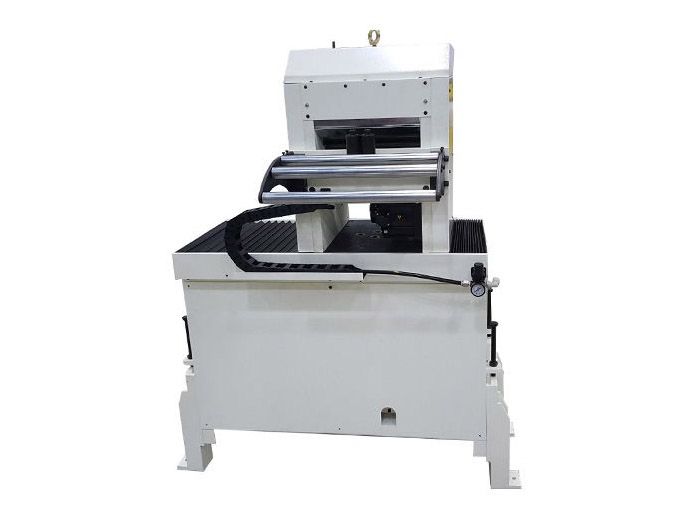
Servo feeders are devices used in various industrial applications for accurate feeding of materials or parts into a production line. They are used in a variety of industries, including automotive, electronics, food processing, and more.
Servo feeders are devices used in various industrial applications for accurate feeding of materials or parts into a production line. They are used in a variety of industries, including automotive, electronics, food processing, and more. In this guide, we will cover everything you need to know about servo feeders, including how they work, their benefits, and how to choose the right one for your application.
How Does a Servo Feeder Work?
A servo feeder consists of three main components: a feeding unit, a control unit, and a servo motor. The feeding unit is responsible for delivering the material or part to the production line, while the control unit regulates the speed and timing of the feeding process. The servo motor provides the necessary torque and rotation to drive the feeding unit.
The feeding unit typically consists of a hopper, a feeding mechanism, and a sensor. The hopper is where the material or part is stored, and the feeding mechanism is responsible for delivering it to the production line. The sensor detects the presence of the material or part in the hopper and signals the control unit to start or stop the feeding process.
The control unit regulates the feeding process based on input from the sensor and other factors, such as the production speed and the type of material or part being fed. It uses a feedback loop to adjust the speed and timing of the feeding process to maintain a consistent flow of material or parts.
The servo motor provides the necessary power and torque to drive the feeding unit. It is controlled by the control unit and rotates the feeding mechanism to deliver the material or part to the production line.
Benefits of Servo Feeders
Servo feeders offer several benefits over other types of feeders, including:
Accuracy: Servo feeders are highly accurate and can deliver materials or parts with precision, which is important in many industrial applications where consistency and precision are critical.
Speed: Servo feeders can operate at high speeds, which can increase productivity and reduce production time.
Flexibility: Servo feeders can be programmed to feed a wide range of materials or parts, making them a versatile option for many different applications.
Efficiency: Servo feeders use less energy than other types of feeders, which can reduce energy costs and improve overall efficiency.
Safety: Servo feeders are designed with safety in mind and often have safety features that prevent accidents and injuries in the workplace.
Choosing the Right Servo Feeder
When choosing a servo feeder, there are several factors to consider, including:
Material or part size: Servo feeders are available in a range of sizes to accommodate different materials and part sizes. It is important to choose a feeder that can handle the size and weight of the material or part being fed.
Production speed: The speed of the production line will affect the feeding speed of the servo feeder. It is important to choose a feeder that can keep up with the production speed to avoid bottlenecks in the process.
Material or part type: Some servo feeders are designed for specific types of materials or parts, such as liquids, powders, or fragile parts. It is important to choose a feeder that is appropriate for the type of material or part being fed.
Control system: The control system is a critical component of the servo feeder, and it is important to choose a system that is reliable, easy to use, and can be customized to meet specific production requirements.
Safety features: Servo feeders should have safety features such as emergency stop buttons, guards, and sensors to prevent accidents and injuries in the workplace.
If you are looking for high quality servo feeder, welcome to contact us for detailed information!