Multi-Blanking and Cut to Length Lines

Applicable material
Material Type: Cold rolled plate, Hot rolled pickling plate, High strength cold rolled plate, Galvanized plate, High strength hot rolled plate etc.
Material Thickness: 2.0-12mm
Coil Width: 200-1800mm
Yield strength: 245-980 N/mm2
Tensile Strength: 392-1180 N/mm2
Coil inner diameter: Φ610mm
Coil outer diameter: Φ1200-Φ1800mm
Loading weight: 20000KG
Coil line configuration
Hydraulic Shear
Conveyor Belt
Automatic Stack System
Multi-Blanking and Cut to Length Lines
Multi-blanking and cut to length lines are industrial manufacturing systems used for the high-speed production of metal sheets or coils. These lines are typically used in industries such as automotive, appliance manufacturing, and construction.
Multi-blanking lines capable of producing multiple blanks of various sizes and shapes from a single coil of material. The materials used from carbon steel to stainless steel, aluminum, and other metals. This system is capable of processing multiple at once, maximizing productivity and reducing material waste.
Cut to length lines are a type of metal processing that cuts metal sheets or plates into specified lengths, typically used in production of trims, strips and flat sheets. These systems are capable of processing a range of materials including Carbon steel, Stainless steel, Aluminum,PVC coated materials, and pre-painted materials. This system can accommodate coils or sheets as raw materials.
Both multi-blanking and cut to length lines are automated systems that can handle high volumes of metal sheet processing. The lines usually consist of uncoilers, straighteners, feeders, leveling equipment, cutting tools, and stackers. These systems are designed for high efficiency, accuracy, and cost-effectiveness, which has made them popular in various industries.
Usually the blanking line is composed by a coil feeding line,a hydraulic shear machine and a stacking system entrusted with the sheet stacking and the successive distribution to the various forming presses installed in the factory.
This blanking line can process comprehensive range operations, applicable metal coil from 2.0mm to 12mm thickness, and width from 200mm to 1800mm.This line has a high synchronization between each workstation, which achieves stable working performance. Integrated with servo control system, it's a high-level industrial automation line, which is easy operation and reduced operational costs.
Main Machine For Multi-Blanking and Cut to Length Lines
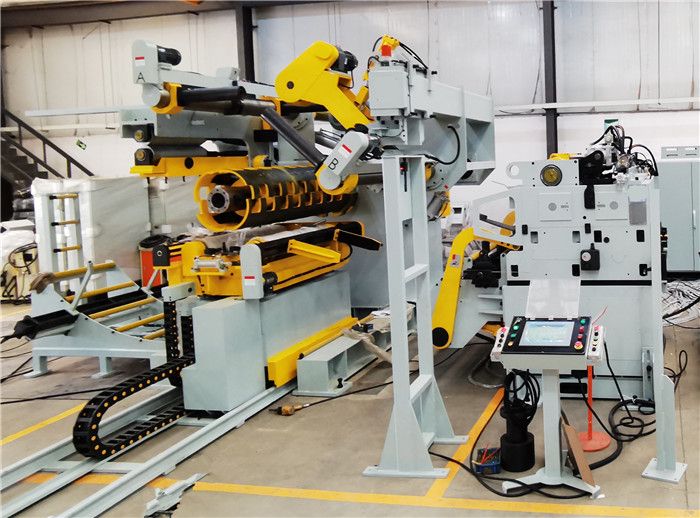
Compact Coil Feeding Line
A compact coil feed line is not only a simple integration of three types of machines: decoiling, leveling and feeding, but also emphasizes highly integrated control in control operations.
The main part of the compact coil feeding line is as below:
1. Coil Car---Hydraulic power, wear-resisting surface
2. Decoiler Mandrel ---Hydraulic Expansion, Delta Inverter
3. Pressing Arm---Coil well-knit, no disperse
4. Limiting Arm--- Locating coil, avoid coil shuffling
5. Support Arm---Auxiliary support coil
6. Coil Inlet---With supporting swing arm
7. Control Cabinet---Weinview Touchscreen
8. Straightening Part---GCr15 steel straightener rolls
9. Handwheel --- Straightening value adjustment
10. Outlet Bracket --- Adjustable length
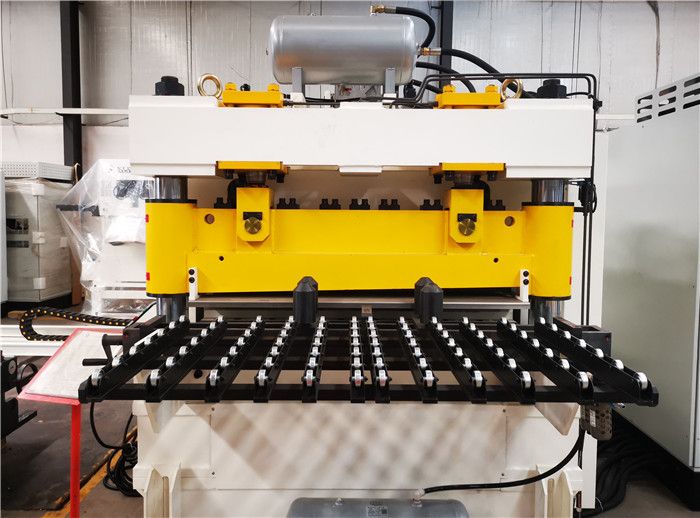
Hydraulic Shear
1. Used for cutting the strips into small pieces.
2. It will be driving by hydraulic motor.
3. Max. Cut Thickness: 0.8-6.0mm, if the thickness is 6-12mm, the hydraulic shear machine will be another structure.
4. Cut gap adjustment: According to different material thickness, manually adjustable shear gap.( material thickness between 2.0-3.0mm, not need adjustment ).
5. Gap value display: Dial indicator display.
6. Blade material:DCW53 (HRC60-62°)
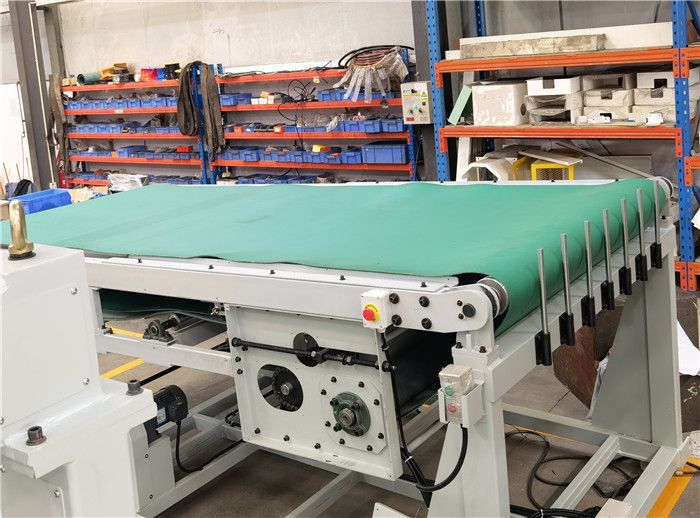
Conveyor Belt
1. Made of roller or rubber belt accoding to the products.
2. Transfer the cutting length parts to the Stacker System.
3. Conveyor belt moves driven by AC deceleration motor with frequency control.
4. Width can be customized according to the open size of the press machine and the size of Max. finished parts.
5. One end of conveyor belt is fixed, and the height of the upper surface of the belt at the other end can be adjusted within ±200, the height is also customized accroding to the center height of the whole line.
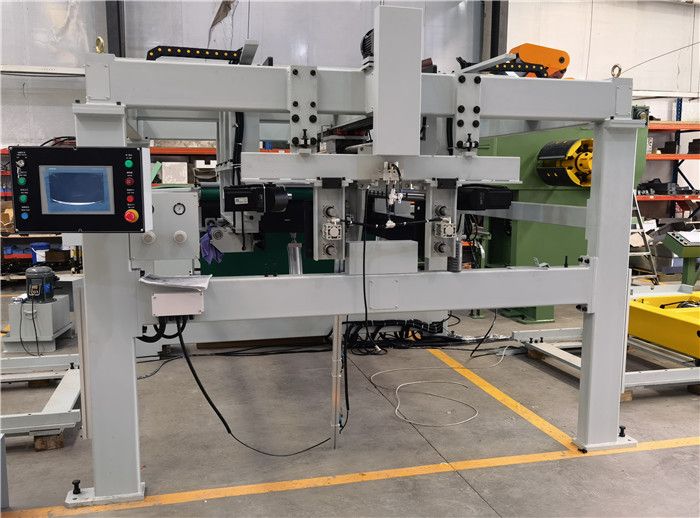
Automatic Stack System
1. Used to automaticaly stacking the cutting products,Combined with lifting platform and trolley, it can also transport neat stacking and chopping steel plates to the packaging area. The device is equipped with feeding device and automatic beating mechanism, which plays a good protective role on the surface of steel plates. In addition, the device has the length and width limit, automatic plate, automatic lifting and other functions.
2. The mechanism is arranged on the right side of the conveyor belt, which is composed of 1 group of hydraulic lifting mechanism, 3 groups of multi-functional flapping device, 2 groups of stacking trolley and 1 console.
3. When it's automatic production, the stacking car moves to the receiving position, and the hydraulic lifting mechanism in the pit will lifting and ready to receive the cutting length sheets, and the same time the cutting length sheet is transferred to the receiving platform by conveyor belt, when the sheets fall down to the receiving platform from the conveyer belt and it will trigger the sensor to control the action of the flapping cylinder, and the action frequency of the flapping cylinder can be set in the system.
4. At the same time of the sheet stacking, the car will gradually drop through the sensor console. When the sheet counting reaches the set value, it will output the signal to stop and wait for the next sheet receiving trolley to drop the material when it reaches the position, and the sheet starts a new round of sheet stacking.